8cj00l新一代航空发动机总共有3 万多个零件,涉及230 多种不同标准的材料,与加工制造相关的特点具体如下:
(1)零件加工精度高
发动机零件要保证在高温、高速、恶劣环境下可靠工作,需要零件具有良好的配合质量和互换性,一方面对零件的加工精度要求极高,很多零件的精度要求都在微米/ 次微米级,非配合表面粗糙度要在Ra1.6 以下,配合表面粗糙度在Ra0.8 以下;另一方面,对设备的加工精度及精度保持性要求很高,还要配套相应的精密检测设备,甚至需要多轴多功能复合加工与检测一体的设备来完成。
(2)多种冷却小孔
航空发动机涡轮叶片、燃烧室、火焰筒等零组件的冷却小孔每台份多达数十万个,而且是异形精密群孔,尺寸在?0.1-0.3mm ,孔的位置呈空间多向分布,其外壁还有涂层。孔的形位精度和孔壁表面质量要求高,常规的钻孔、冲孔方法难以满足要求,需要激光、电子束、电火花等特种加工技术和装备。
(3)零件表面特种工艺要求多
为了提高发动机零件的耐磨、防腐蚀、抗疲劳性能,需要采用表面强化、喷涂、喷丸、渗镀等表面处理技术与装备。涡轮导向叶片、燃烧室采用的陶瓷热障涂层,尤其是涡轮叶片表面高温防腐蚀涂层,其
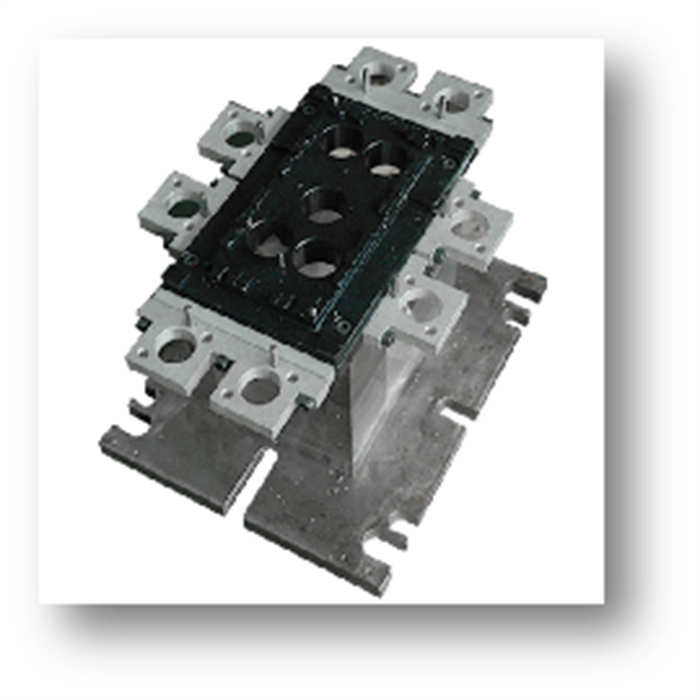
在实际加工中刀具的选择应考虑以下几个因素:工件材料、工件形状、加工要求、加工机床、系统刚性以及表面质量技术要求等。
以涡轮机匣零件为例:
1. 从工件材料上分析,变形高温合金、铸造高温合金等难加工材料大量采用,这些难加工材料导热系数小、强度大、切削温度高,易产生加工硬化,切削时刀具磨损快,刀具寿命短,刀具消耗量大,因此必须合理选择刀具几何角度。
2. 从工件结构上来看,壁薄、刚性差、难加工。加工零件凸起部分时,刀具系统容易与零件、夹具干涉,因此,必须对刀具路径进行优化,如插铣加工代替侧铣,空行程快速走刀,优化抬刀位置,采用螺旋插补等方式进行铣削。
3. 从加工工序上分析,机匣需要经过粗加工、半精加工、精加工,为了节省刀具费用,在制造这类零件时,粗加工时可采用高性能陶瓷铣刀,半精加工和精加工时采用标准硬质合金刀具和非标高性能专用刀具,这样可显著提高生产效率。
4. 从加工经济性方面上来说,刀具配置方案需要不断改进,尽量采用刀具商最新研发的产品。
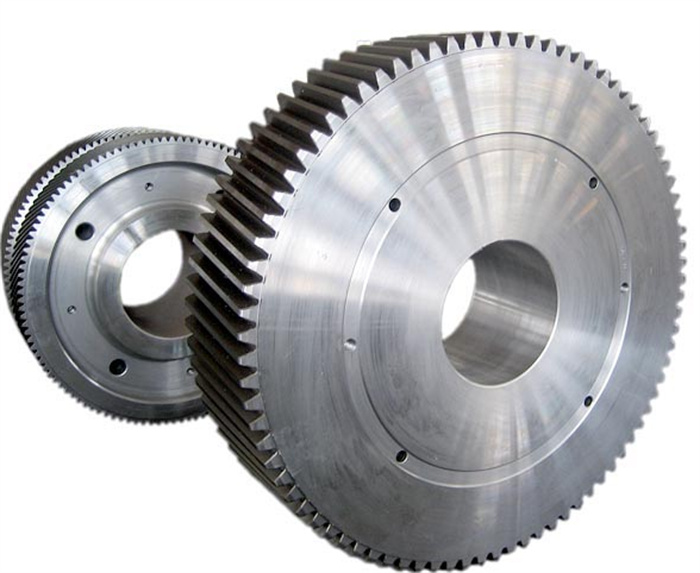
航空发动机的涡轮盘、整体叶盘、涡轮叶片等零件的材料大多为钛合金和镍基高温合金,如图所示,由于大多是薄壁件,因此对其制造精度要求极高,对其加工刀具要求亦很高。高温合金加工时由于其切削力大、加工硬化倾向大、切削温度高、刀具磨损严重使其成为典型的难加工材料。
高温合金家族共有的特点:导热性差、弹性模量小、化学活性高和摩擦系数大,还具有其他高温合金不具备的高强度、高韧性和高硬度的特点使得其归属于难加工材料行列。在车削过程中主要表现在切屑与前刀面接触面积小,刀尖应力集中,切削温度高,切屑不易折断并且锯齿化严重,刀具磨损严重,导致加工效率很低,工件加工表面质量较差。