8cj00l汽车模具尺寸错误或厚度不足:
错误的尺寸会导致汽车模具直接报废,不能使用,因此在模具制作之前,操作人员一定要进行仔细的测量与计算,合理分析之后再开始铸造过程。而厚度不足可能会导致模具原材料不足,但是这种缺料情况可以根据堆焊来进行解决。

汽车模具高速切削工艺的研发
(1)切削机理的研究
高速切削技术发展的时间短,切削机理方面还有很多内容仍需要进一步的研究和完善,主要表现在由于速度大幅提高,过程中产生的切削力、切削热、刀具磨损状况以及表面情况都将与传统对应因素所产生的现象和造成的结果显著不同。
(2)切削参数的优化
在设备、材料、加工策略一定的情况下使用合理的参数将大大提高效率,并做到效率和质量的最佳组合。因此在高速切削方面进行参数优化是提高效率和质量的一个重要技术环节。
(3)切削策略的研究
成功进行高速切削的重要前提是承受近乎恒定的切削载荷,在这种条件下能够保证良好的高速切削效果。针对切削复杂曲面需要进行过程中去除材料体积变化小、切削载荷恒定的策略研究以避免刀具较快的磨损和减小让刀误差。
(4)切削数据的建立
高速切削数据库存储高速切削参数等数据供查询和使用,在管理工艺数据进行工艺规划方面起着重要作用。为促进企业稳定持续发展,建立针对高速的切削数据库势在必行。
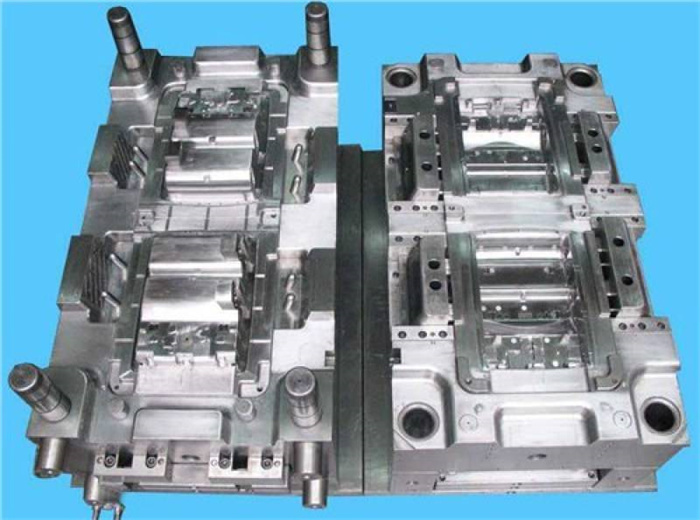
高速汽车模具制造的工艺优势
(1)提高制造速度
高速切削以高于常规切削数十倍左右的切削速度对汽车模具进行高速切削,由于高速机床主轴激振频率远远超过“机床—刀具—工件”系统的固有频率范围,汽车模具高速切削过程平稳且无冲击。用高速数控中心或高速铣床制造汽车模具,可以在工件一次装夹中完成型面的粗、精工和汽车模具的其他部位,即所谓“一次过”技术。高速切削技术的使用大大提高了汽车模具的开发速度。
(2)提高模具精度
由于采取了极小的步距和切深,汽车模具的高速切削工艺可获得很高的表面质量,甚至可以省去钳工修光的工序。
(3)简化制造工序
常规切削只能在淬火之前进行,淬火造成的变形必须要经手工修整最终成形。而通过高速切削来完成不会出现表面硬化的问题。另外由于切削量减少,高速可使用更小直径的刀具对更小的圆角半径及模具细节进行切削,节省了部分修整工序从而缩短了制造周期。
(4)简化修复过程
汽车模具在使用过程中往往需要多次修复以延长使用寿命,如果采用高速切削工艺可以更快地完成修复,取得以铣代磨的效果,而且无需重新编程,且能做到精确无误。