清水混泥土墙面明缝施工
明缝是对清水混凝土整体表面进行分块处理, 从而达到建筑结构与外观装饰艺术统一的建造技术。施工缝应与每设一道水平明缝相吻合。明缝的设计尺寸2*1cm,安装模板时固定在竹胶板上,明缝要求线条顺直、平整光滑,在混凝土施工时以附在模板上的嵌明缝条而形成。为选择合适的嵌条材料, 我们综合比较了木条、不锈钢条、塑料条等几种材料,最后决定选用质量性能较好、便于安拆的塑料条。为便于明缝条的脱离,将明缝条加工成斜角企口状,并在明缝条表面涂抹脱模剂或黄油。
清水混泥土墙面禅缝施工
禅缝是在清水混凝土表面精心设计的有规则的装饰线条,可表现出规律和韵感之美,由模板拼缝形成,它比明缝更进一步地对表面进行分割及装饰。必须综合考虑模板的规格、施工安排、饰面效果等。模板拼缝不严密、模板侧边不平整、 相邻模板厚度不一致等问题都会造成拼接缝处漏浆或错台,影响禅缝观感质量。
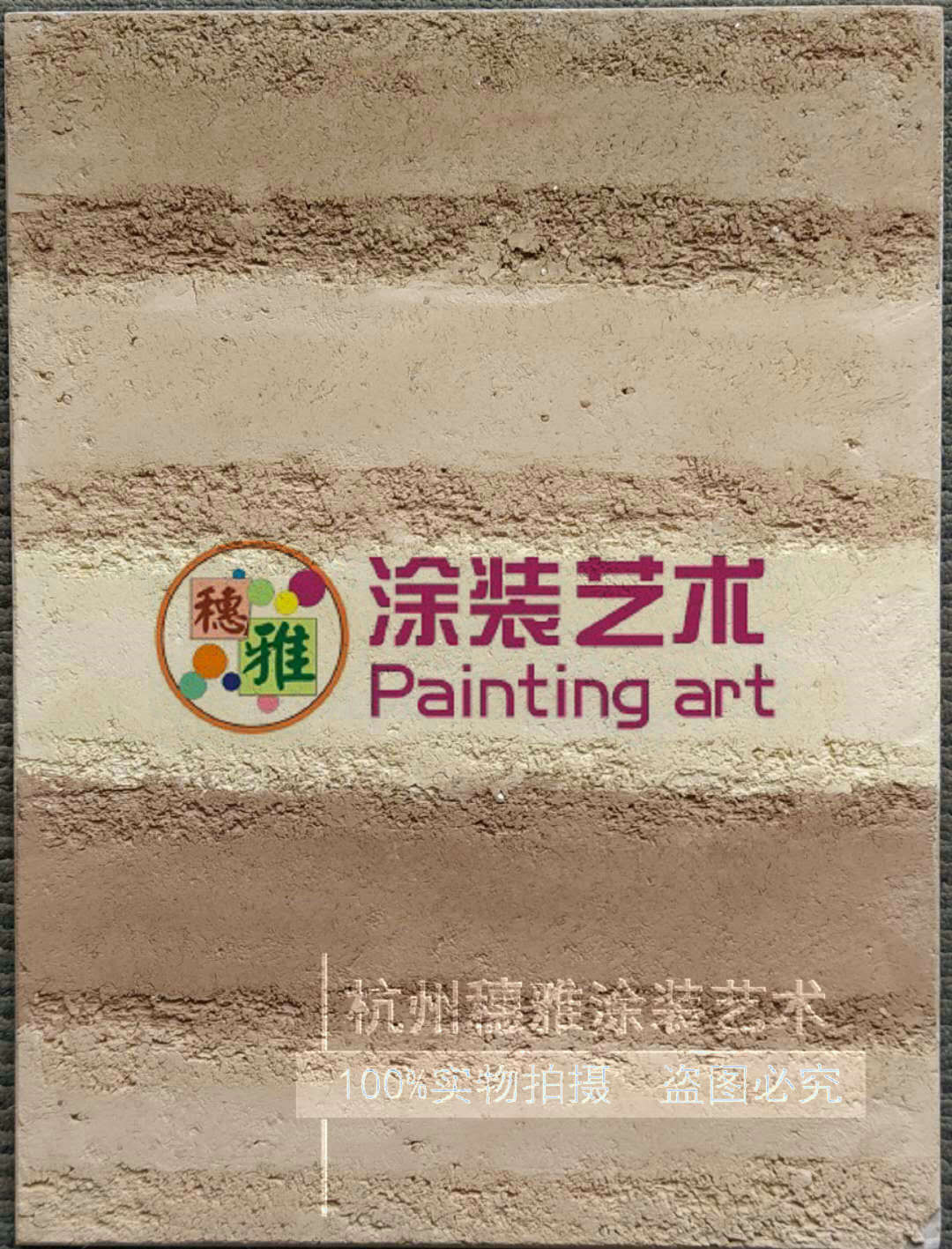
技术领域
本发明涉及夯土墙的施工技术领域,特别是涉及高强度夯土墙的夯筑方法。
背景技术
针对夯土墙建筑,传统的夯筑方法大致包括以下几个工序:材料准备—支模—倒入材料—捣实—夯实—拆模;由于现代社会科学的技术的发展,传统做法的夯土墙施工进度非常缓慢,并且对墙体的强度以及垂直度只凭借夯土工人的经验去辨别,没有科学依据,墙面容易出现参差不齐的胀膜、漏夯等现象,达不到当代人对外观的要求,又不能保证施工的质量。传统夯筑方法在施工过程中没有高空安全措施,存在一定的安全隐患,这不满足现代建筑的施工要求。这种做法既影响了美观,又违反建筑施工的原则。
传统夯筑模板主要有两类。类是采用3块木板制作而成,两侧模板长1.5米左右,端部挡板的宽度同墙厚,侧模之间采用可拆卸的木棍夹住,侧模与端部挡板之间通过榫卯连接并卡紧,模板高度一般为30-33厘米,使用这种模板夯筑的墙体通常叫做'板筑墙';第二类是采用表面光滑顺直的圆木代替两侧木模板,一般每侧有3-5根圆木,当一层夯筑完成后,将最下层的圆木翻上来固定好,用同样的方法继续夯筑,依次一根一根上翻,循序进行,使用这种模板夯筑的墙体叫做'椽打墙'。
然而,'板筑墙'虽然操作简单,但是受本身结构形式所限,模板尺寸无法做大,导致每版完成墙体高度、长度尺寸均较小,影响了墙体的整体性,且由于采用纯木制作,木板易变形易损坏。'椽打墙'由于采用圆木,因此夯筑的墙体表面凹凸不一,极不平整。由于其自身形式问题,不得不采用收分的办法以保证墙体的稳定性,即墙体断面自下往上尺寸逐渐减小。同时由于没有固定的端头模,导致夯筑时墙体尺寸误差较大。而且这两类模板还存在一个共同缺点,即只能夯筑一字型墙体,无法解决相邻墙体的一次性夯筑,使得相邻墙体间会产生明显的竖缝,对房屋的整体性造成很大影响。
发明内容
本发明提供一种操作简便、安全系数高、能保证施工质量和美观程度的高强度夯土墙的夯筑方法。
解决的技术问题是:传统夯筑方法和模板支设方式不能满足对墙体强度和美观度的需求,施工质量不易控制,施工安全没有保障。
为解决上述技术问题,本发明采用如下技术方案:
本发明高强度夯土墙的夯筑方法,包括以下步骤:
步骤一、材料准备:将白灰与黄土加水拌合,搅拌均匀形成灰土原料,充分熟化后加入糯米浆进行拌合;每立方米灰土原料中加入糯米浆90-110kg;
步骤二、支设模板:采用脚手架支撑模板,并以对拉螺栓固定,完成模板支设;
步骤三、倒土:将步骤一制得的材料倒入步骤二支设好的模板内;
步骤四、夯筑:采用7kg方夯进行一次夯筑,然后采用10kg圆夯进行二次夯筑;
步骤五、逐层夯筑:重复步骤二和步骤四,进行逐层夯筑;
步骤六、养护和拆模:完成墙体夯筑后,进行薄膜覆盖养护;养护后,进行拆模;
步骤七、墙面美化:拆模后留在墙体上的对拉螺栓通洞,对其进行填塞,在墙体两侧进行拍土直至与墙体具有相同的密实度;所用材料与夯土墙材料相同;
步骤八、墙面固化:待墙体干燥后,在墙体表面喷洒固化剂。
本发明高强度夯土墙的夯筑方法,进一步的,步骤一中白灰与黄土的质量比为3:7。
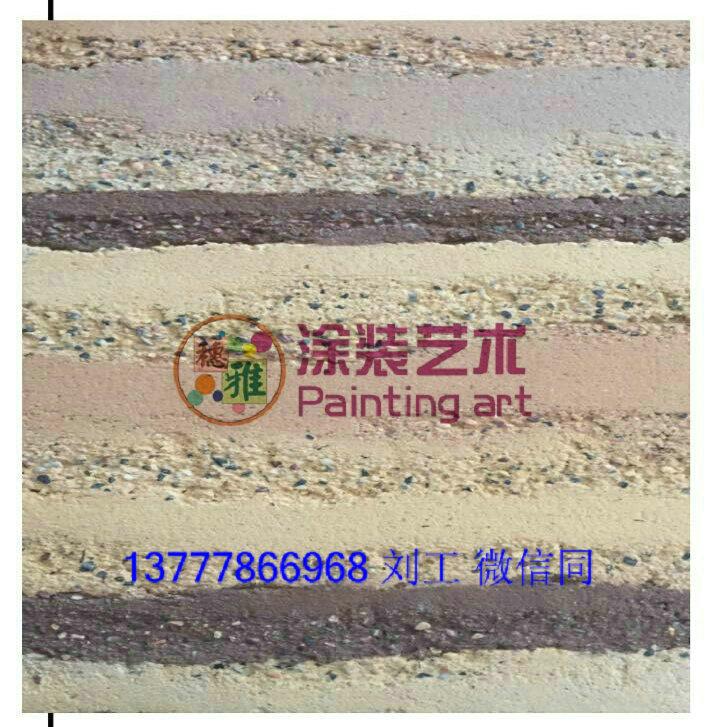
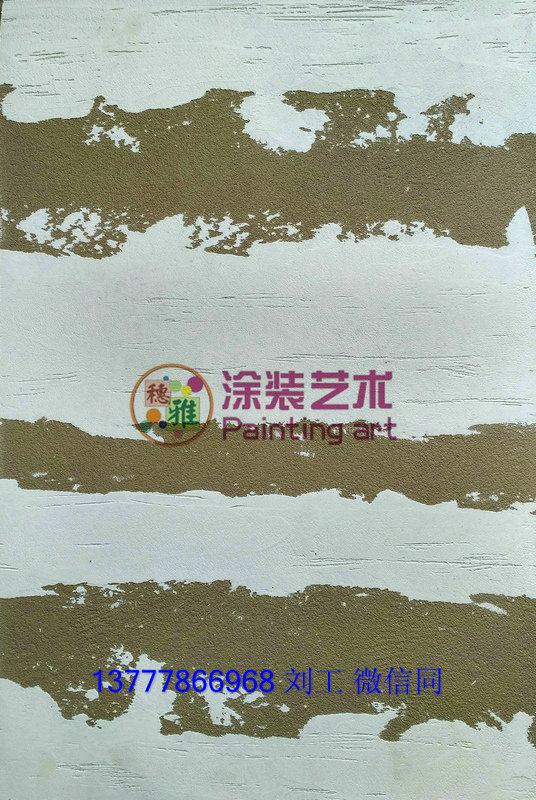
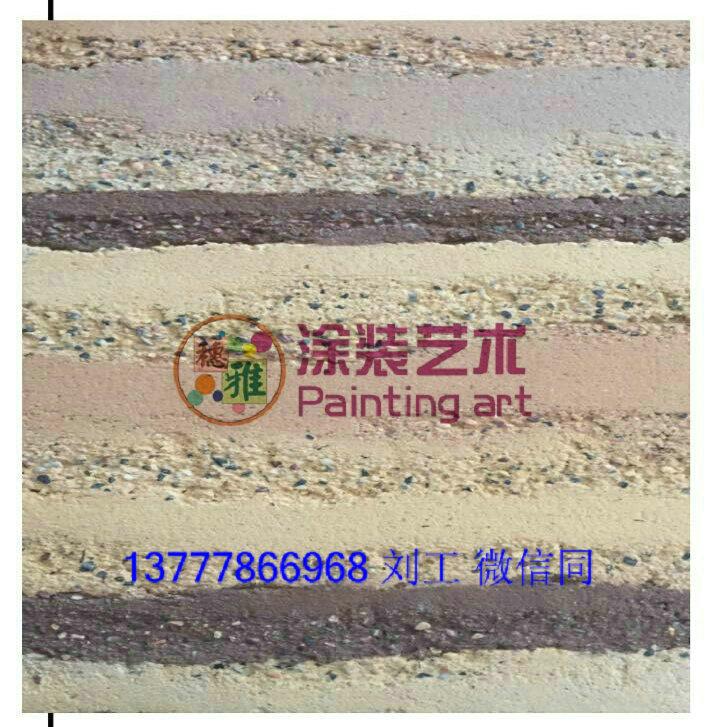